A large manufacturing plant in Auckland relies on a complex network of pipelines for various functions. One such pipeline, an 80NB air line, is critical for the overall plant’s operation. When a valve for the line failed, meaning this line could no longer be isolated without massive production disruptions, an innovative solution was required: the 80NB Hot Tap and Line Stop.
The Challenge: Critical Air Line Maintenance without Disruption
The challenge lay in replacing the isolation valve without causing costly disruptions to the plant’s operations. Traditional methods would involve shutting down the entire air supply system across the plant, leading to production downtime and substantial financial losses. The manufacturing team needed a solution that would enable them to replace the valve, while maintaining air supply to the rest of the plant.
The Solution: Guaranteed Flow Systems Ltd – 80NB Hot Tap and Line Stop
Enter the innovative Guaranteed Flow approach of the 80NB Hot Tap and Line Stop. This method involved creating a new 80NB branch connection, or “hot tap,” directly onto the 80NB air line while maintaining its operational integrity. In conjunction with this, a line stop was implemented to temporarily halt the flow of air within the pipeline, enabling valve replacement work to be carried out.
Key Steps
Feasibility Study and Planning: The project commenced with an extensive feasibility study to ensure that the hot tap and line stop approach was suitable for the plant’s air line. This phase involved analysing pipeline specifications, operational requirements, access, and potential risks.
Thorough Planning & Testing: The Guaranteed Flow team carried out a series of workshop tests to simulate the live situation and to identify and eliminate costly risks to the operation. When the hot tap and the main line are the same size, it is essential that the fabrication and operation are executed with precision to avoid causing damage during the hot tap.
Line Stop Implementation: The line stop technology was employed to create a temporary barrier within the 6 bar air line. This allowed the valve replacement to proceed without affecting the overall air supply to the plant.
Maintenance and Inspection: With the line stop in place, maintenance teams could safely perform replacement of the faulty valve.
Completion and Restoration: After the valve replacement was completed, the line stop was removed, and the hot tap connection was seamlessly integrated into the air line. The entire process was carried out with minimal disruption to plant operations.
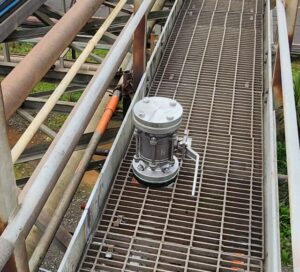
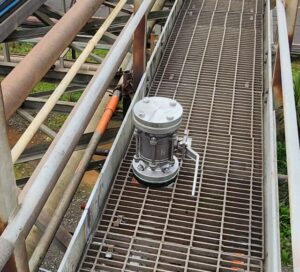
Results and Impact
The successful execution of the 80NB Hot Tap and Line Stop at the large manufacturing plant delivered remarkable results:
Minimal Downtime: By employing this innovative technique, the manufacturer was able to avoid production downtime that would otherwise be required with traditional maintenance methods.
Cost Savings: The avoidance of prolonged production disruptions translated to substantial cost savings for the manufacturer.
Operational Benefits: The maintenance and restoration of an isolation valve for the 80NB air line ensures continued operational efficiency, maintaining the plant’s output at optimal levels.
Proven Innovation: The project demonstrated Guaranteed Flows commitment to innovation and its ability to leverage advanced solutions to address critical challenges.
In conclusion, the successful implementation of the 80NB Hot Tap and Line Stop at the large manufacturing plant stands as a testament to the power of innovation in industrial settings. By addressing critical maintenance needs without compromising operational continuity, Guaranteed Flow showcased its adaptability and commitment to excellence in the face of challenges. This case study serves as an inspiration for other industrial facilities looking for creative solutions for difficult problems.